Radial chip thinning is a phenomenon that has been well understood for decades. It is the simple observation that when the stepover is 50% of the tool’s width or greater at a given feedrate, the width of chips remains constant.
However, when the step-over is less than 50%, the chip width becomes progressively smaller as the stepover decreases
Why is it important to know this? Because most of the heat generated in the tool and the steel part is removed, not by coolant, but by the chips. If you decide (for good reasons) to use stepovers smaller than 50%, you will need to run at a faster feed rate to get the chip thickness back up to target. If you are not cutting at the targeted chip thickness, your heat management will be off because the chips do not have the mass needed to retain the heat, pull it away from the tool and part, and put it into the chip pile.
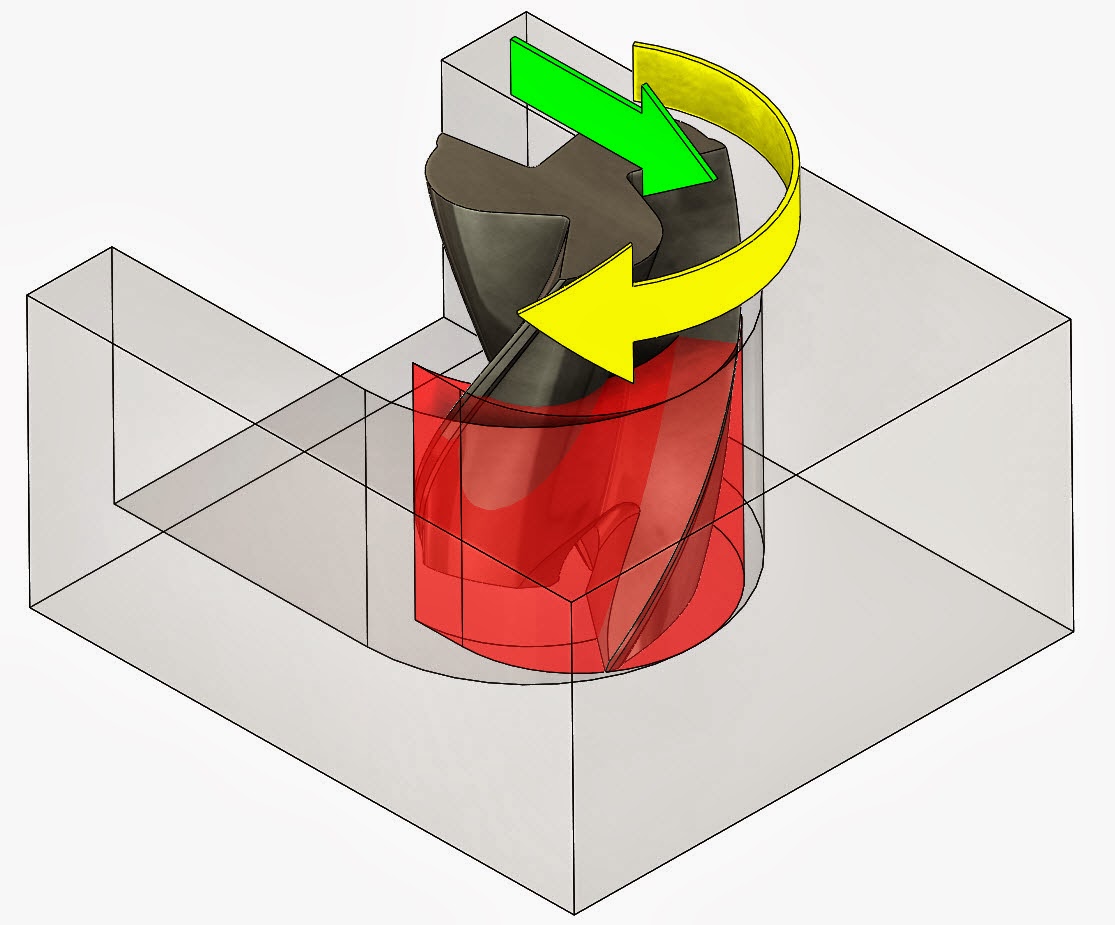
Chips are the primary driver of heat removal. Traditional cutting yields larger chips with good heat removal capacity.
Here is one practical application of this knowledge: Say you are programming a part to run at 35 in/min at a 50% stepover, but the tool may be long or the material very tough, so you decide to run a little bit lighter on the tool by reducing the stepover to 30 or 40%. To compensate for the thinning effect, you should look up and set a higher feed rate, using tables readily available on the Internet.
This will produce two benefits–you will cut the part a little faster and these settings will do a better job maintaining your targeted chip thickness leading to better heat management. A far more important and game changing application of this knowledge is the use of Mastercam’s Dynamic Motion technology to improve productivity and reduce tooling wear and costs.
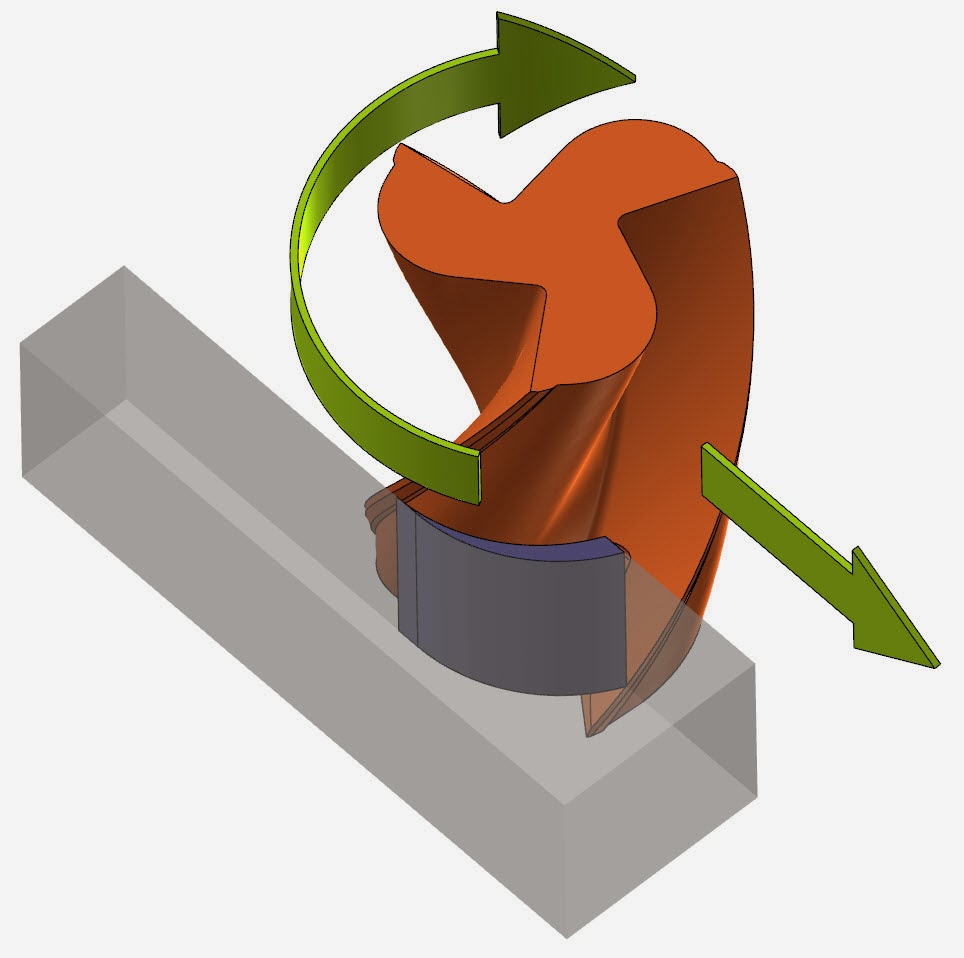
Smaller stepovers require higher feed rates to maintain your targeted ship thickness, and can yield faster cut time.
Many manufacturers obtain impressive productivity improvement by employing Dynamic Motion strategies in combination with today’s advanced cutting tools. Radial chip thinning is easily implemented. A discussion with your tool vendor and Mastecam Reseller can help you choose appropriate tools, cutting strategies, and radial chip thinning parameters for your applications.