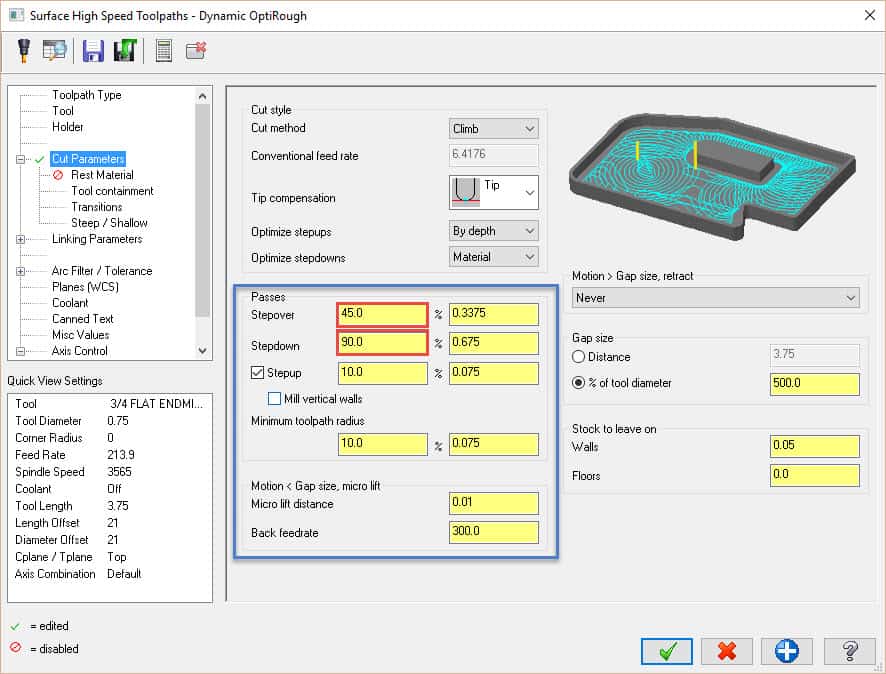
Dynamic Machining is one of Mastercam’s Core Competencies. As many of you have done in the past, lots of our customers call in with issues regarding the best utilization of their machines. With regards to Mastercam, this means making sure the Dynamic Motion is always used as smoothly as possible. Below there are a few steps that should help you on your way to making sure all the proper toolpaths are put in place.
Mastercam’s high speed Dynamic milling toolpaths utilize the entire flute length of their cutting tools to gain greater efficiency in milling. they are designed to maximize material rates while minimizing tool wear.
Benefits to gain from using High speed Dynamic tool paths include:
1. Tool burial avoidance
2. Minimal heat buildup
3. better chip evacuation
4. Wear is distributed along entire tool cutting length
5. Faster roughing times.
Dynamic Milling Parameters
Seen in the Diagram these are the parameters to make your machine successful using the dynamic tool paths.
1. Stepover: This is the radial engagement of your tool, At any point your tool will never exceed this percentage. 35-45% stepover is a recommended as a base line.
2. Step down: Very similar to depth cuts in our contour tool path, this uses a percentage or hard number to control the depth of cut. Our recommend starting at no less that 4 X D to ensure success. Stepover and Stepdown are the two parameters that make the dynamic tool path work so efficiently. Used correctly can greatly reduce cycle times and Tool wear.
3. Stepup: Very similar to Stepdown, When cutting 3D shapes the step up will give you a reduced Cusp height when roughing angles, radius and similar features.
4. Minimum Tool path radius: Acts as the twin to step over, It controls the how small of a radius you want to cut. For just roughing large amounts of material you can increase this number to cut cycle time but could require additional operations to rough to desired amount.
5. Micro lift distance & Back feed rate: at any point the tool is not engages into the work it will lift up (micro lift) and feed back to it starting engagement position. We recommend using double the programmed feed rate for back feed. But no less that the initial programmed federate.
Thanks for taking a moment to explore common tech questions with us at QTE. Don’t forget to stop by our training landing page, https://qtemfgsolution.wpengine.com/training/ to see what kind of training would be best for your Implementation. Also remember, ALWAYS check with your tooling vendors before fully setting up the Dynamic Motion Parameters to ensure you do not crash your machine or snap a tool!
Check back in next week when we feature another of our Top 10 Tech Questions to help you run more efficiently!